Two of the most critical methods for the PCB assembly process are: Surface Mount Technology (SMT) and Through Hole Mounting (THM). While SMT places components exactly on the surface of the PCB, THM employs leads inserted into holes drilled in the PCB and soldered on the other side.
Modern, compact devices depend on SMT since it makes more components possible to be assembled automatically. Long-standing and effective in creating strong mechanical connections, THM has been utilised for high-reliability applications.
Originally first seen in the 1940s, THM dominated PCB manufacture until SMT arrived in the 1980s. SinceSMT reduced costs and improved performance, it altered the way electronics were manufactured..SMT became the ideal approach for compact and high-performance devices; But still THM stands as the top choice where electrical circuits are robust and last a long period. In this blog, we will walk you through a comprehensive analysis of both THM and SMT so that you can choose the right one for the manufacturing process.
Key Highlights
- Surface Mount Technology (SMT) is the process of physically mounting electronic components onto the surface of PCBs.
- Through-Hole Mounting (THM) is the process of placing electronic components with leads through pre-drilled holes on the printed circuit board.
- The main pros of SMT and THM are efficiency, reliability, and mechanical automation while the cons are complicated maintenance, less design freedom, and large setup costs.
- Labour intensity is lower for SMT while it is higher for THM.
- SMT comes up with high initial costs but is more cost-effective in the long run as compared to THM.
- While choosing the right technology, you must consider the project specifications, future proofing, and environmental issues.
What is Surface Mount Technology (SMT)?
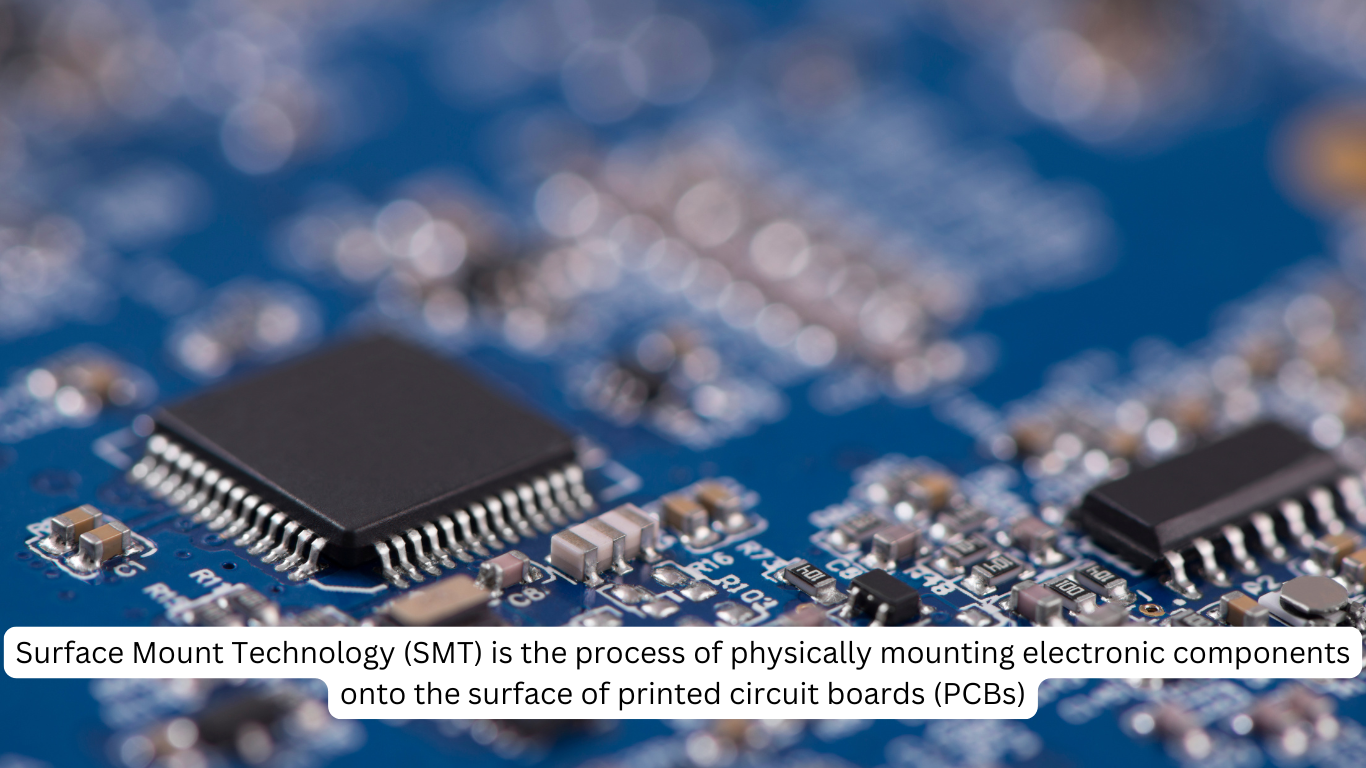
Surface Mount Technology (SMT) is the process of physically mounting electronic components onto the surface of printed circuit boards (PCBs). This technique involves automated machines mounting Surface Mount Devices (SMDs) on the PCBs surface. Then,the PCB with components is passed through a reflow oven, where solder paste melts to form electrical connections between SMDs and PCB pads. After soldering, PCBs undergo Automated Optical Inspection (AOI) to guarantee appropriate component placement and solder connections.
Types of SMDs
Common Surface Mount Devices (SMDs) used in SMT include resistors. They provide resistance in circuits and are available in various sizes. Then, there are capacitors. These components store and release electrical energy which is crucial for filtering and energy storage.
Next is integrated circuits (ICs). These complex circuits miniaturised into single packages, including microcontrollers and memory chips. Also, there are diodes. They allow current to flow in one direction, used for rectification and signal modulation. And transistors are used for amplification and switching.
Applications
SMT is widely used across various industries due to its ability to support miniaturisation and high-density assembly. In consumer electronics such as smartphones, laptops, and wearable devices use SMT for their space-restricted designs. They are also popular on portable medical equipment and diagnostic tools.
Along with that electronic control units (ECUs) and infotainment systems in the automotive industry depend on SMT for their reliable performance. That’s why these components are also used in telecommunications such as network routers, switches, and modems.
What is Through-Hole Mounting (THM)?
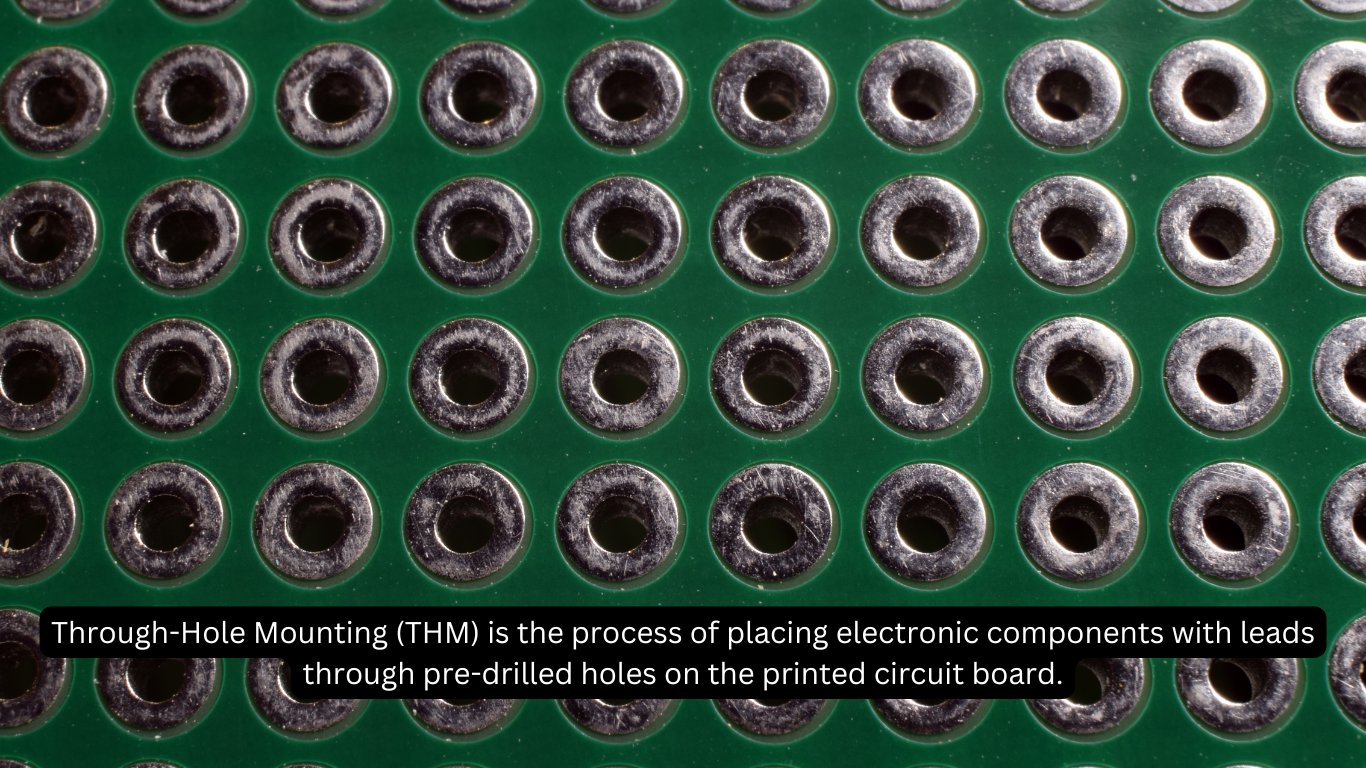
Through-Hole Mounting (THM) is the process of placing electronic components with leads through pre-drilled holes on the printed circuit board. This technique involves various steps.
1) Component Insert
Components with axial or radial leads are manually or mechanically inserted into the drilled holes on the PCB. Then, the leads that protrude through the holes are connected to the other side of the PCB using either wave soldering or manual soldering. After soldering, the connections are checked for dependability and sufficient electrical conductivity.
2) Component Types
Commonly used through-hole components include Axial Leaded Components such as resistors, capacitors, and diodes. They have leads extending from each end, allowing them to sit flat on the PCB.
Electrolytic capacitors and LEDs have leads projecting from one side and are vertically mounted on the PCB. Various connections used to link different PCB areas or external devices. Transformers are used in power supply circuits to transform and isolate voltages.
3) Applications
Through-Hole Mounting is preferred in specific applications because of its mechanical strength and durability. High-Reliability Applications include aerospace, military, and industrial equipment where durability and long-term performance are essential.
Prototyping enables easier hand assembly and customization during the development process. THM are also found in power electronics. Because, here components require more robust mechanical bonding to withstand higher currents and voltages.
Pros of SMT and THM
Both SMT and THM have several similarities. Here are some of the positive reasons why manufacturers mainly pick either of them:
1) Efficiency
Smaller and more compact designs emerge from SMT components being employed on both sides of a printed circuit board (PCB), hence augmenting component density. This preserves a great deal of room.
Since SMT components are smaller and automated assembly techniques make them more affordable for mass production. This is so since labour and material expenses are lowered.
2) Dependability
THM is a suitable material for uses requiring strong connections since of the lead insertion and soldering through the PCB, which can offer strong mechanical bindings. High-stress applications including aerospace, military, and industrial uses requiring reliability find THM components appropriate.
3) Mechanical Automotion
Since SMT lets for faster and more exact component positioning, it is perfect for automated assembly operations. Productivity thus rises and becomes more constant. By reducing the necessary manual labour, SMT's automated features lower the chance of human error and raise general manufacturing efficiency.
Cons of SMT and THM
- Smaller and more closely packed, SMT components are harder to change or fix. These parts need particular tools and knowledge to run, which complicates maintenance and updates.
- THM components need holes to be drilled into the PCB, which takes up valuable space and limits the possibility to arrange parts on both sides of the board. Less effective, more bulky designs can result from this restriction.
- Comparatively to SMT, the need for through-holes limits layout choices and complicates multilayer PCB designs, which results in less design freedom.
- Since SMT allows for automated assembly, which lowers labour costs and boosts output, it is more cost-effective for big volume manufacturing. But, the initial setup and equipment expenses for SMT could be more, though.
Differences in Assembly of SMT and THM

1)Assembly Process
Surface Mount Technology (SMT)
- Solder Paste Application: First, manufacturers apply solder paste to the pads using a PCB stencil.
- Component Placement: Then, automated pick-and-place machines position the SMDs onto the solder paste.
- Reflow Soldering: Now, the PCB is passed through a reflow oven where the solder paste melts and solidifies. It creates electrical connections.
Through-Hole Mounting (THM)
- Drilling: At the beginning, holes are drilled into the PCB for component leads.
- Component Insertion: Then, components are manually or automatically inserted into the drilled holes.
- Soldering: After that, the PCB goes through wave soldering or manual soldering to secure the components.
2) Equipments Required
Surface Mount Technology (SMT)
- Stencil Printer applies solder paste to PCB pads.
- The Pick-and-Place Machine automatically places SMDs onto the PCB.
- Reflow Oven melts the solder paste to form electrical connections.
- Automated Optical Inspection (AOI) inspects the PCB for defects.
Through-Hole Mounting (THM)
- Drilling Machine drills holes for component leads.
- Wave Soldering Machines perform soldering components in bulk.
- Manual Soldering Tools are used for manual assembly and repairs.
- Test Equipment is required for checking solder joints and connections.
3) Labour and Time
Surface Mount Technology (SMT)
- Labour Intensity is lower due to automation, reducing manual labour needs.
- Time Requirement is dropping. Because, now faster assembly is possible due to automated processes, suitable for high-volume production.
Through-Hole Mounting (THM)
- Labour Intensity is higher due to manual component insertion and soldering.
- More time is required. Because slower assembly is more suited to low-volume production and prototyping.
Cost Comparison Between SMT and THM
a) Production Costs
Surface Mount Technology (SMT)
Modern technologies and automation in small-scale manufacturing cause greater initial setup costs. But as volume rises, the cost per unit drastically lowers once the setup is finished. Large-scale manufacturing is quite affordable for mass production since fast automated processes lower labour costs and boost efficiency, thereby saving money.
Through-Hole Mounting (THM)
Small-scale manufacturing lowers starting setup costs, so it is more affordable for small batches or prototype runs where human assembly is feasible. However, in big-scale manufacturing, big volumes are less cost-effective for which manpower costs and slower production speeds apply than SMT.
b) Material Costs
Surface Mount Technology (SMT)
Usually smaller and less costly than through-hole equivalents, SMT components help to save materials. Effective use of PCB space reduces the need for bigger boards, so lowering the material costs.
Through-Hole Mounting (THM)
Because of higher material and production complexity, through-hole components are usually bigger and more costly. Drilled holes require more space, hence bigger and more costly PCBs could follow from this.
c) Maintenance and Repair
Surface Mount Technology (SMT)
Because of their small size and density, which often call for specialised tools and experience, repairs can be more complex and costly. Changing or reworking PCB components can be time-consuming and physically demanding, therefore raising maintenance costs.
Through-Hole Mounting (THM)
Larger and more easily available components simplify repairs and changes. Reduced maintenance and repair costs follow from this. THM is more appropriate in environments needing regular maintenance since components may be rapidly desoldered and replaced.
How to Choose the Right Technology for Your Project?
The technology you apply determines the simplicity of the manufacturing process. Here are some things to consider before choosing a specific manufacturing technology:
1) Project Specifications
Needs for Functionality
Review the particular tasks your project calls for. Usually SMT is the superior option if high-density, small-sized design and fast assembly are top concerns. THM could be more suited for projects requiring strong mechanical strength, such those involving heavy-duty applications or power electronics.
Manufacturing volume
SMT can be automated, it is more affordable for large-scale manufacturing; THM may be more affordable for small-scale or prototype manufacturing because of reduced setup costs.
2) Environmental Issues
Operating Conditions
Think of the surroundings in which the goods will be used. THM provides more mechanical bond strength. So, it is better for high-stress situations such as mechanical stress, heat cycling, or substantial vibration.
Space Constraints
For portable and space-restricted applications, SMT enables greater component density and double-sided PCB assembly if the project calls for a small design with limited space.
3) Future Proofing
Upgradability in Nature
Evaluate future changes and improvements' simplicity. Because THM components are simpler to replace and rework, they are a superior option for designs that might call for regular upgrades or repairs.
Technological Advancements
Think about the long run availability and support for the technology. SMT guarantees that your project stays relevant and current with future technical developments since it follows contemporary trends toward downsizing and high-speed assembly.
Conclusion
While both Surface Mount Technology (SMT) and Through Hole Mounting (THM) are methods to assemble PCBs, each has advantages and drawbacks. The decision between SMT and THM should rely on the requirements of the project, including the degree of room availability, the surroundings, and the production capacity. Miniaturisation and automation will probably help SMT become more well-known over time. New hybrid technologies, however, could be able to incorporate the finest aspects of both approaches, allowing more adaptability in future solutions.