As its name reveals, a prepreg is nothing more than an insulating film. The heat transfer allows prepreg–a dielectric material—to be inserted between two cores or a copper foil and core in the preparation of PCB, to provide the required insulation. It acts as the bonding layer between copper-clad laminates in multilayer PCBs for both electrical insulation and physical support. Prepreg is responsible for tuning the desired electrical properties such as controlled impedance depending on their dielectric constants. The mechanical properties are also reinforced to keep the PCB reliable and durable.
Prepreg, in multilayer PCB designs some bonding agent that comes between layers so as to secure the stability and reliability of a stack-up. The application of it influences the final performance, providing minimal signal loss and higher performance for high-frequency applications. The dielectric properties required by the PCB developer mean that a specific thickness and resin content were necessary, so using prepreg was essential in order to design any given layer of customised stack or laminate having desired electrical as well mechanical features. These are the reasons that the global prepreg market is expanding 12.5% annually.
Key Highlights
- Prepreg, short for pre-impregnated material often refers to the fibreglass cloth that has been impregnated with resin which is used in Burn-IN boards making.
- Prepreg is prepared after going through a serious of steps like impregnentation process, drying and curing, custting and packaging, and controlling the resin.
- You must consider singla integrity, thermal stability, and resin type before choosing the right prepreg.
- Prepreg is a semi-cured fiberglass material impregnated with resin while laminate refers to fully cured fiberglass sheets with copper cladding on one or both sides.
- The different types of prepreg are FR4 Prepreg, High Tg Prepreg, PTFE Composites, polyamide prepreg, and nonwoven aramid prepreg.
What is PCB Prepreg and Why is It Essential?
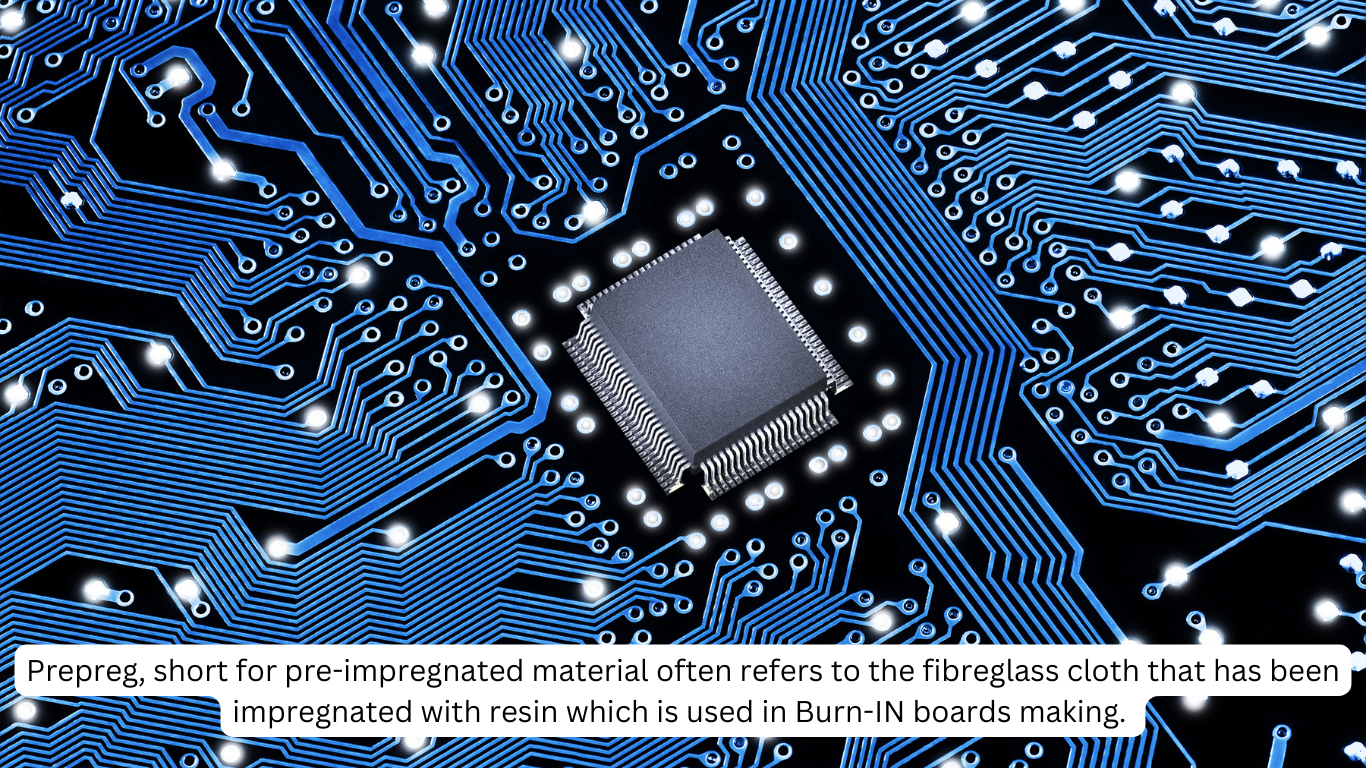
Prepreg, short for pre-impregnated material, often refers to the fibreglass cloth that has been impregnated with resin which is used in Burn-IN boards making. Prepreg: A composite material containing two fundamental constituents
Fibreglass Fabric: The purpose of this woven material is to add structural integrity which keeps the prepreg in place.
Resin (typically epoxy): Many manufacturers receive the fabric with a partially-cured resin system already on it, which is typical for epoxy(resin), this material state can be referred to as B-stage. This state of partial curing enables the prepreg to soften and flow under heat and pressure during the PCB lamination process, bonding it with other layers. It also acts as an electrical insulator in the conductive layers.
Significant importance of Prepreg in Multilayer PCBs
The use of prepreg is critical for success creating a multilayer PCB because achieving the necessary stability and alignment in a multi-layer stack would be almost impossible without it. For multilayer PCB fabrication, prepreg is essential for the following reasons.
Layer Bonding: Prepreg works as the adhesive, bonding copper layers and insulating materials together in a multilayer PCB stack-up. Without this bond, the PCB would not be structurally sound in a multi-layer design and unusable.
Dielectric Properties: One of the most important—and common—things prepreg helps you control in a PCB is dielectric constant. This affects the way signals are transmitted and is crucial in high-speed or high-frequency PCB applications that require fine tune-ability of signal integrity.
Thickness Customization: Because prepreg comes in different thicknesses and therefore different resin contents, manufacturers can control the amount of dielectric material between each layer.
Function of Prepreg in the Adhesive of PCBs
In the lamination process, the partially cured resin of prepreg is softened under heat and pressure where it will fill gaps between layers to bond them together as a single PCB. This keeps the different layers in line so that they are bound together, which allows for more strength and durability. The property of the prepregs being adhesive is what makes multi-layered PCB designs possible while maintaining their stability over time in operation.
How PCB Prepreg is Manufactured
The manufacturing process must be both comprehensive and exact to assure the final prepreg for PCB meets or exceeds modern standard requirements from a circuit board fabrication standpoint. Even the smallest mistake made in each operation, from impregnation to cutting and packaging of prepreg can lead to compromised performance for multilayer PCBs.
1. Impregnation Process
This process makes a prepreg, which also acts as an adhesive and dielectric by coating the fibreglass fabric with resin. Because the high-grade polyester resin coats a fibreglass fabric, impregnation must be carefully controlled to ensure an even depositing of resin across each layer.
Fibreglass Fabric Preparation: The operation described here is focused on what is called the reinforcement material or support fabric which gives mechanical strength; This fabric is generally woven to a density dictated by designed mechanical properties for the prepreg product.
Bath of epoxy resin: The fibreglass passes through a bath of epoxy resin with perhaps some additives to improve the properties, such as flame resistance or flexibility. Although the composition of resin can vary depending on application, for optimal insulating and bonding epoxy is most popular.
Partial Curing (B-staging): Resin is partially cured (to the B-stage). At that point, the resin is tacky and not completely cured which permits it to flow in a laminating press during PCB assembly that helps make strong interlayer connections.
2. Drying and Curing
After impregnation, the next steps applied for drying and curing to ensure that resin is well cured and maintained its bonding ability in lamination. This is an essential stage in the regulation of a perfect final prepreg material.
Controlled Drying: The drying concerns the controlled one to which occurs a quick entrance of these resins. It extends on this wire passing through an oven specifically designed for this process. The temp and time inside the drying oven are controlled to be unvarying all over the prepreg for partial curing.
Partial Cure Monitoring: It is important to understand the level of cure as overcure makes a metamorphic transition during lamination difficult, meanwhile under-curing will not provide bond strength. Hence, accuracy in this stage is crucial for the overall quality of prepreg.
3. Cutting and Packaging
After the resin has been cured to specification, it is trimmed and packaged into rolls of prepreg for sale. This pre-shipment is intended to prepare the materials for correct use in PCB manufacturing.
Precision Cutting: The next stage is precision cutting of the prepreg which has dried by now and partially cured (solid-state polymerization). Precise cutting is necessary to enable the prepreg sheets to be aligned perfectly with one another during PCB layering so defects will not appear in the finished product.
Sterile Prepreg Sheets: Prepreg sheets are tagged with epoxy resin content, fibreglass type and thickness. Now for the prepreg, we need to pack it as well in order that we make it clean and uncontaminated before PCB fabrication.
4. Controlling Resin Content
When making a prepreg, one of the most important variables to control is resin content as it has a significant impact on mechanical and electrical properties. Having the right resin-to-fibre ratio allows you to adjust your prepreg for specific designs on PCBs.
Adjusted Resin Amount: The amount of resin is precisely controlled in the impregnation stage since this will affect significantly on final properties of prepreg. More resin offers greater adhesion and insulation, so this is used for high-frequency or higher-speed operations.
Strength and Flexibility: Similarly, on the other extreme is low resin content which makes stiffness so rigid that it can result in less deformation under stress for higher mechanical strength requirements. Developing the resin-to-fibreglass ratio, however not to an excessive extent, is another critical process in PCB production. It gives manufacturers room where they can fine-tune their prepreg for certain mechanical and electrical performance requirements.
This creates a structured system of prepreg manufacture that makes the material ideal for various PCB applications, while ensuring mechanical robustness and electrical performance.
Choosing the Right Prepreg for PCB Design and Fabrication
Making sure the prepreg in use for a PCB design is the right one is even more crucial as it directly impacts on following performance, durability and reliability of desired product. The prepreg must meet a number of different criteria: its choice has to take into account the application-specific requirements with respect to signal integrity, thermal stability and material compatibility.
1. Signal Integrity and Dielectric Constant (Dk): Signal integrity is one of main issues for high-speed and high-frequency applications. The dielectric constant (Dk) of the prepreg can have an influence on how signal propagates in the PCB. Low Dk: Signal loss and crosstalk, are greatly reduced by decreasing the associated capacitances between signal layers. It is important to choose prepreg materials with consistent dielectric properties so that signal integrity is maintained throughout all the PCB layers.
2. Thermal Stability and Glass Transition Temperature (Tg): Prepregs are the type of material that is chosen for their thermal stability, which plays a significant role in PCBs because most PCB experiences high temperature during operation or soldering. The second condition is the temperature refers to it as of glass transition (Tg) that is point in degrees centigrade where the resin changes from being hard and stiff, what we call rigid, to a more flexible state. High Tg prepreg is sought after in applications where the system will be running at higher temperatures to maintain board flatness and minimize deformation when subject to thermal stress.
3. Resin Type and Compatibility with PCB Stack-Up Materials: The resin in the prepreg must also be consistent with all other materials present within the PCB stack-up, such as core laminates and copper layers. Use of epoxy-based resins are versatile for many material and mechanical properties, however, more distinct resin — such as polyimide or PTFE may be mandatory to provide better performance in thermal/mechanical/ chemical resistance. It is for this reason that it is important to try and match the coefficients of thermal expansion (CTE) between prepreg plies, in order to avoid delamination or cracking when the part has experienced a number of temperature cycles.
Designers can achieve maximum PCB performance, reliability and lifetime by choosing the right dielectric constant, Tg and resin type with prepreg carefully. It all comes back to this alignment of material properties with design goals that is necessary for a long-lasting and functional multilayer PCB.
Understanding Resin Content and Its Measurement in Prepreg
The resins found in prepreg are of great importance as they establish the performance, reliability and durability expected from a Printed Circuit Board (PCB). This resin, besides bonding the layers together, is also a dielectric material that provides insulation between them and therefore affects the electrical characteristics of PCBs. It is very important to reach the correct resin content for managing efficiently as a gap filler in between layers and safeguard of uniform mechanical, electrical properties.
1. Importance of Resin Content in Prepreg :
The resin content directly impacts several key performance factors:
- Adhesion and Bonding: The right resin content ensures a strong bond between the layers, preventing delamination while providing structural stability.
- Dielectric Properties: The resin serves as electric insulation. Insufficient resin can also lead to inadequate insulation leading to signal degradation or cross talk while overdoing it could cause the board not hold its dimensions.
- Mechanical Properties: Resin content controls the mechanical strength of a PCB that determines how easy it is to be deformed and withstand thermal stress. Too much and warping or cracking may result during processing, as well in operation.
2. Measuring Resin Content
Resin content values are of great importance to accurate measurement and quality control in prepreg manufacturing. Two common methods are:
Burnoff Tests: In this method, a piece of prepreg is baked to burn off the resin; i.e., leaving only behind glass fabric. A difference in weight before and after burning is the level of resin there.
Thermogravimetric Analysis (TGA): TGA monitors the weight loss of sample and is typically performed under a controlled atmosphere as it heats. However this way is more accurate and gives the option of a deeper analysis or resin content along with thermal profolings.
3. Ensuring Uniformity and Consistency
The uniformity and consistency of layers in a PCB is vital for high-performance applications, requiring control over the resin content. This feature ensures that an even resin flow throughout the layers leads to consistent electrical properties, which in turn helps signal integrity and lowers defects such as void or misalignment. Having a uniform resin content, it will help us obtain the same mechanical properties on every point of the PCB which make our boards stable during lamination.
The mechanical and electrical performance of multilayer PCBs can be improved by maintaining the proper resin content, measurements using appropriate methods.
What is Resin Flow in Prepreg and Why Does It Matter?
The corrected resing flow is athermic frieze, it need that has been caged by the pre-preg expelled to move. When it heats up, the resin melts and under pressure, flows in between edges of PCB layers stitching them together to prevent electric spark generation. Resin flow is such important attribute, designed to provide a bond with high integrity and continuity that prevents voiding while meeting both the electrical properties of the PCB according design standard as well mechanical ones.
Controlled resin flow is the most important value-added process in order to maintain a certain quality as well reliability of a final PCB While low resin volumetric flow can lead to delamination and is responsible for a bad layer-to-layer adhesion, Conversatorily, too high the resin flow may result in excess adhesion which could lead to a push-out of the same and hence mis-registration between layers or changes in thickness or disruption on dielectric properties.
Factors influencing resin flow include:
- Temperature: Higher temperatures increase resin fluidity, promoting flow during lamination.
- Pressure: Adequate pressure ensures proper resin distribution between layers but must be controlled to avoid overflows.
- Type of Resin: Different resins have varying flow characteristics, impacting their suitability for specific PCB designs.
Controlling these factors is crucial for achieving consistent, high-quality PCBs that meet performance standards.
Comparing Prepreg and Core: Key Differences
Prepreg and core are two essential materials used in PCB fabrication process, each with distinct roles. Understanding their differences is critical for designing high-performance, reliable PCBs.
1. Core The core is a rigid dielectric material with copper layers on both sides, fully cured and ready for use as a foundation in multilayer PCBs.
- Structural Integrity: The core provides the PCB with its mechanical strength and stability.
- Electrical Properties: Copper layers within the core manage signal transmission and electrical performance, forming the base of the circuitry.
- Location in PCB: Typically used as the central layer or one of the middle layers in a multilayer PCB stack-up.
2. Prepreg Prepreg is a semi-cured fiberglass material impregnated with resin that acts as a bonding agent during lamination.
- Bonding Function: Prepreg softens and flows under heat and pressure, bonding layers together and filling gaps.
- Dielectric Insulation: It insulates electrically active traces between layers, helping to maintain signal integrity.
- Role in Multilayer Design: Prepreg is applied between the core and additional layers in the PCB, ensuring that layers adhere properly during the lamination process.
3. Common Misconceptions
- Not Interchangeable: Prepreg and core are often mistaken as interchangeable, but they serve distinct roles—core provides structure, and prepreg bonds layers together.
Joint Influence on Performance: Another misconception is that prepreg alone dictates the board’s electrical performance. In fact, both core and prepreg contribute to the final mechanical and electrical properties of the PCB.
Prepreg vs. Laminate: Understanding the Distinction
In PCB construction, prepreg and laminate serve distinct roles. Understanding these differences is key to ensuring proper PCB performance and reliability.
1. Prepreg Prepreg is a semi-cured fiberglass material impregnated with resin, used to bond layers together in multilayer PCBs.
- Bonding Function: Prepreg softens and flows during the lamination process, creating a strong bond between layers and filling any gaps.
- Dielectric Insulation: It insulates the electrically active traces between layers, helping maintain signal integrity.
- Used Between Layers: Prepreg is primarily used in the internal layers of a multilayer PCB stack-up, acting as an adhesive between core layers.
2. Laminate Laminate refers to fully cured fiberglass sheets with copper cladding on one or both sides, forming the structural base of the PCB.
- Structural Strength: Laminates provide the PCB with its overall rigidity and durability.
- Conductive Surface: The copper-clad surface of the laminate is etched to create the conductive pathways needed for circuit connections.
- Outermost Layers: Laminates are typically used as the outer layers of the PCB, housing the external circuitry and electrical components.
3. Implications of Incorrect Usage Using the wrong type of prepreg or laminate can have significant impacts on PCB performance.
- Improper Prepreg: Insufficient bonding due to incorrect prepreg can lead to delamination and affect dielectric properties, resulting in signal loss or interference.
Wrong Laminate: A mismatched laminate may cause warping, cracking, or failure under thermal stress, jeopardizing the PCB’s overall stability and functionality.
Choosing Between Core and Prepreg in PCB Design
Core and prepreg are both important in PCB design, but they have different significance when it comes to a targeted structure of the printed circuit board. The core is a solid material throughout, consisting of fully cured reinforced fiberglass in an epoxy resin matrix that has copper cladding on one or both sides. It provides the basic structural strength and electrical footing for this PCB. However, one of the things I had to learn real quick was why prepreg or FR4 + 2116 is not a metal; it is smeared out glass and resin that sits between layers in multi-layered PCBs.
1. Roles in PCB Structure
Core — forms the central layer of an entire PCB stack-up, it provides mechanical strength and support for copper traces that deliver electrical signals.
Prepreg: Acts as the bonding agent between core and other layers providing dielectric insulation properties but must have good adhesion strength with different beams.
2. Impact on Design Factors
- Signal Integrity: The core provides a good stable to make copper traces land, which is very important for the line signal integrity. It is also an injectable dielectric to help isolate the layers from each against preventing crosstalk. The prepreg choice can also affect the absolute dielectric constant, which may have a greater effect on path lengths of board traces at high speeds as it influences how fast signals travel.
- Control the Impedance: Maintaining Core thickness & Prepreg dielectric constant are major factors in controlling impedance. Corresponding selection of prepreg ensures that impedance is the same on every layer, which is very important for design route signals by time and needs continuity.
- Thermal Management: Core materials typically have better thermal stability whereas a control in prepreg processing must be coordinated to avoid blistering or warping at the operating temperature due to its susceptibility of non-homogeneity.
3. Tips for Selecting the Right Combination
- Application Requirements: Use a low dielectric loss core with ultra-high speed or radio frequency (RF) applications to maintain signal integrity by pairing that high-performance time constant board material with the same type of prepreg.
- COUNT OF LAYERS: Complex multilayer designs should choose a prepreg that has the ideal resin flow control and an adjacent heat expansion coeff for no delamination effect.
Thermal: For heat sensitive applications, make sure your core and prepreg materials can handle the operating temperatures without degradation/performance issues.
Properties of PCB Prepreg
The fibre materials used and the resin systems will decide mechanical, electrical or thermal properties of PCB circuit laminate. These properties are designed to fulfill the different needs and uses of several PCB applications.
1. Types of Fiber Materials in Prepreg
Glass Fiber: Most used material fiber in prepreg, glass fiber provides good strength and stiffness along with electrical isolation. Renowned for its high-temperature stability and moisture resistance, this dielectric is well-suited to standard PCB applications.
Aramid fiber: second only to glass, aramid fibers (at commonly known as Kevlar) take the prize for their high strength-to-weight ratios and decent thermal stability. They are flexible and widely used for the applications which demand lightweight, shock resistant PCBs.
2. Resin Systems in Prepregs
- Epoxy Resins (Standard): Most commonly used resin system in pcb prepregs, epoxy resins balance strength, impact resistance and glass transition temperature with relatively low cost. Prepregs made from epoxy are inexpensive and the enterprise standard for general PCB usage.
- Polyimide Resin: Polyimid is ideal for use in high-performance PCBs that need more thermal stability and chemical resistance. These prepregs are more expensive and able to withstand higher temperatures than epoxy.
- PTFE (Teflon) Composites: The unique qualities of PTFE prepreg fibers have made them a common choice in high-frequency applications. They are excellent but can be difficult to handle for the very properties that make them great insulators in RF and microwave PCBs.
3. Additional Elements
- Weave Styles: The fiberglass weave pattern in prepreg affects the mechanical strength and flexibility. The tighter the weave, the more rigid; looser weaves allow for improved resin flow and flexibility during lamination.
- Aerial Weight: It is the weight of fiberglass per unit area. Higher aerial weight means more fiberglass, potentially leading to increased mechanical strength but reduced flexibility.
- Filler Particles: Basalt fillers can be used as fuels to improve specific properties, such as flame resistance, mechanical strength or dielectric performance.
- Flame-retardants: in order to meet the safety requirements (such as, UL94-V0) and since prepregs are a resin system they must contain flame retardant materials that prevent both ignition of the composite or spreading fire in operation.
Different Types of PCB Prepreg
PCB prepregs come in various types, each tailored to specific applications based on thermal, mechanical, and electrical performance requirements.
1. FR4 Prepreg: FR4 is the most commonly used prepreg, composed of woven glass and epoxy resin. It provides a balance of strength, dielectric properties, and flame resistance, making it ideal for standard multilayer PCBs.
- Use: General-purpose PCBs, consumer electronics, and industrial applications.
2. High Tg Prepreg: High Tg (glass transition temperature) prepreg is designed for applications requiring higher thermal stability. It withstands greater temperatures without softening or degrading.
- Use: High-temperature environments, automotive, and aerospace PCBs.
3. PTFE Composites (Teflon): PTFE-based prepregs offer superior dielectric properties and low signal loss, making them ideal for high-frequency and microwave applications.
- Use: RF, microwave, and high-speed PCBs.
4. Polyimide Prepreg: Polyimide prepregs are known for their excellent thermal stability, chemical resistance, and durability. They are suitable for high-performance and extreme-environment applications.
- Use: Aerospace, military, and high-performance computing.
5. Nonwoven Aramid Prepreg: Aramid fibers offer high strength-to-weight ratios, impact resistance, and good flexibility, making them suitable for lightweight and flexible PCB designs.
Use: Flexible PCBs, lightweight electronics, and applications where impact resistance is needed.
Guidelines for Choosing PCB Prepreg Types
- FR4 for a typical case: For most standard multilayer PCBs, FR4 prepregs will ideally suit, as cost friendly and balanced performing materials. This makes them popular in consumer electronics, industrial controls, and other general-purpose devices.
- Use high Tg for thermal stability: Where your board will be operating at elevated temperatures, as you'll find in automotive and aerospace applications or with some power electronic devices, the use of a high Tg prepreg ensures that your circuit boards survive under these conditions.
- Choose PTFE for high-frequency applications: If you have needs that include the passing of RF and microwave circuits, then using a PTFE prepreg can help to reduce signal loss and make sure your device performs electrically optimum.
- Choose polyimide for the harshest conditions: If you are designing a product that will be exposed to high temperatures, chemicals, or mechanical abuses in environments such as aerospace and military and even computers of better performance; preimpregnated materials made from polyamide offer enough adhesion.
- Nonwoven: Ideal for flexible, lightweight designs. Use nonwoven aramid prepregs in applications that require a suitable degree of flexibility and lightness while maintaining resistance to impact loads (e.g., wearables electronics, foldable devices as well as several other types of next-generation consumer gadgets.
Best Practices for Handling PCB Prepreg
The proper handling and storage of PCB prepreg is very important for keeping its quality so that you can get the best results during your PCB fabrication process. Since the resin in prepreg is only partially cured, it reacts to environmental conditions such as temperature, humidity, and handling procedures.
1. Storage Conditions
When you store your prepreg, it is best to keep them in a controlled atmosphere so that they do not dry out.
- Storage temperature: Between 4°C and 23°C (40°F to 73°F) is the ideal. Prepreg can be stored at cold e.g. refrigerating temperatures cooling down the curing aging to over shelf time. Do not over-cure resin by exposing prepreg to higher temperatures.
- Moisture: Prepreg should be stored in a low moisture environment ideally below 50% relative humidity. Too much moisture in your pre-peg can weaken the resin and fiber matric, resulting in poor adhesion between layers causing potential delamination during lamination.
2. Shelf Life Prepreg has a limited shelf life, typically between 3 to 6 months, when stored in ideal conditions. The shelf life depends on the resin system used, with some materials lasting longer than others. To ensure prepreg is used within its recommended time frame:
- Track Inventory: Implement a first-in, first-out (FIFO) system to prioritize older stock for use.
- Expiration Dates: Clearly label prepreg with expiration dates and conduct regular checks to ensure expired materials are not used in production.
3. Pretreatment Processes Before using prepreg in PCB fabrication, it is essential to allow the material to acclimate to room temperature if stored in cold conditions.
- Acclimation: Remove prepreg from cold storage and allow it to sit at room temperature for a minimum of 4 hours before use to prevent condensation and moisture absorption.
- Handling: Avoid excessive bending or flexing of prepreg sheets to prevent fiber damage, which could impact the material's performance during lamination.
Prepreg in PCB Fabrication
Prepreg is an important material in PCB (especially multi-layer board) fabrication. As mentioned before, it is used on the stack, which allows sheets of prepreg to be placed between copper-clad laminates for bonding during a lamination process. The resin present in the prepreg becomes soft and flowable under heat and pressure while laminating helps to fill gaps, leading to strong adhesion between the layers A rigid and uniform PCB structure is formed by this process.
1. Contribution to Mechanical and Electrical Properties
- Mechanical Properties: Applying prepreg improves the structural stability of PCB and maintains its firmness under external mechanical stresses that come from bending, or thermal expansion during operation. It also adds to the general essence of durability and lifespan for a PCB.
- Dielectric Insulation: One of the most important features hindered by prepreg is that it serves as a dielectric insulation between copper layers thereby ensuring controlled impedance and signal integrity. For high frequency PCB applications, the dielectric constant of a prepreg should be chosen judiciously in order to avoid signal loss and also prevent crosstalk between traces.
2. Common Challenges and Solutions
- Regulating Resin Flow: The resin flow while lamination needs to be controlled as it would lead to accurate bonding. One example of this is lamination temperature and pressure control. Flow that is too low can cause weak bonds, and flow that's too high causes layers to slip.
- Layer Alignment: Ensuring that PCB layers are perfectly aligned when the stackup is being done. This is achieved usually by means of alignment pins and manual manipulation more layers may shift if not properly handled before lamination.
- Prevention of Voids: Depression in the prepreg layers moisture-absorbed or wrong lamination. While storing prepreg in a controlled environment (low humidity and cool temperature) helps with this risk, you can eliminate it altogether by allowing your material to acclimate before use.
Conclusion
Picking the right prepreg is essential in order to maintain a PCB that performs well, meets quality standards and is durable. Prepreg is a bonding and dielectric agent, which enables to keep the boards mechanically stable with proper electrical properties of parts. By recognizing the different types of prepreg, their construction materials and resin systems, manufacturers can optimise PCB components for signal integrity (layer quality), thermal management (via copper weight or material choice) and desired overall structural strength. This includes the problems of misalignment and voids which are common when best practice is not adhered to ensuring that this final PCB can succesfully operate under difficult environmental conditions.
Table of Contents
What is PCB Prepreg and Why is It Essential?
How PCB Prepreg is Manufactured
Choosing the Right Prepreg for PCB Design and Fabrication
Understanding Resin Content and Its Measurement in Prepreg
What is Resin Flow in Prepreg and Why Does It Matter?
Comparing Prepreg and Core: Key Differences
Prepreg vs. Laminate: Understanding the Distinction
Choosing Between Core and Prepreg in PCB Design
Properties of PCB Prepreg
Different Types of PCB Prepreg
Guidelines for Choosing PCB Prepreg Types
Prepreg in PCB Fabrication
FAQs
1. How does prepreg selection influence the PCB fabrication process?
Prepreg selection plays a critical role in determining the quality, integrity of lamination bond and heat dissipation on PCBs. This is important to be sure that the resin will flow properly between each lamination, giving strong bonds and minimising chances of delaminations and voids. The dielectric properties are part of the electrical performance, particularly in high-frequency designs where both impedance and signal losses can be influenced by the relative permittivity. Choosing prepreg with the right Glass Transition Temperature (Tg) for thermal management allows PCB consumed operating heat, not bending or cracking during use.
2. What causes prepreg related defects in PCBs?
Problems including delamination, resin starvation and voids in the prepregs lead to errors with PCB reliability which subsequently takes its toll on performance.
Delamination: It is a fault where the PCB layers set apart as their grip is not strong enough. Things that are often the cause of this issue: Resin flow on lamination wasn't good enough, moisture contamination or prepreg is oldest a year. Prevention: store the prepreg properly, control lamination temperature and pressure, use new preparation materials to improve bonding.
Resin Starvation: In this scenario, lack of resin inside the prepreg to fill the regions between layers results into poor adhesion. Prevention: Choose prepreg with a sufficient amount of resin for your type of board and carefully manage how the layers are laminated together so that they get the resin through them properly.
Voids: Voids are little air bubbles caught inside the PCB layers, for the most part brought about by dampness retention or helpless overlay conditions. Prevention: Store prepreg in a desiccant cabinet, pre-acclimate the sheets before the lay-up and be sure to provide even heat and pressure during curing.
Corrosion can be controlled by managing the storage conditions and lamination parameters, which in turn help manufacturers to keep it under shape and thus prevent defects.
3. How to select prepreg thickness for impedance control?
Making sure to choose the correct prepreg thickness for impedance control in PCB designs matters so that signal integrity can remain intact and not degrade with high-frequency applications. Here are key guidelines:
Target Impedance: Begin by defining the target impedance of the design, whether that be 50 ohms for a single-ended trace or perhaps 90 ohms for differential pairs. This will help identify the dielectric constant (Dk) and thickness required.
Calculate the Trace Width and Spacing: A prepreg thickness shall be selected depending on copper trace width spacing. Impedance increases with larger prepreg layers and it decreases when the layer is thin. Having proper trace geometries as well the right prepreg thicknesses are essential for hitting your target impedance requirements.
Choose Accessible Prepreg with a Constant Dielectric: A Change in our prepreg dielectric, the speed of the particular signal differs during propagation. Select a low and stable Dk prepreg material to maintain consistent impedance between different signal layers.
Some may use impedance calculators for PCB: Relate prepreg thickness, trace width and dielectric constant using appropriate simulation model. This helps in getting the proper impedance by adjusting thickness.
4. Does prepreg resin content affect PCB cost?
Yes, it can increase the cost of manufacturing a good deal. Higher resin content also tends to raise material costs—gel coats increase bonding strength, and available dielectric properties can be optimized, which is necessary in high-speed boards. Moreover, the high-resin prepregs are increasingly difficult to manufacture as more skill and precision is required in lamination steps, from which an additional cost arises. Nevertheless, the choice of correct resin content improves PCB performance and thereby decreases risks such as delamination or voids, allowing higher yields with fewer reworks. And although the initial cost of obtaining that level may be higher, initially spending on ideal resin contents could potentially save in longevity by enhancing product reliability and performance.
5. What is the difference between prepreg and laminate?
Prepreg is a combination of fibreglass material and resin that has been half cured, it will be laminated to hold the incredible layers between PCB layers when we apply pressure while doing lamination. It serves as both the mechanical bond and the top level of dielectric insulation between layers. Laminate, meanwhile, is a cured form of fibreglass with copper cladding on both or one side at the sheet level that makes up the PCB structural and conductive layers.
In a PCB, laminate provides the structural strength to the overall board and it is what holds all layers in place with prepreg to help them bond together, making sure not to get separated from each other. The copper-clad circuit traces are the base for electrical performance, while prepreg insulation between conductive layers impacts signal integrity through dielectric properties and impedance control. Choosing the correct combination of prepreg and laminate is essential to provide mechanical durability as well as electrical functionality in the final PCB.