In this video, Anoop B Sridhar (Product Manager, Fintech Space), Prithvi Raj Narendra (Founder, Appiko Technologies) and Murali Srinivasa (Founder, LionCircuits) are going to talk about Design for manufacturing and it’s importance to inculcate it at the early stages of the manufacturing process.
Anoop: Welcome to TechLite! Our Vlog/Podcast to everything Tech. We are bringing to you a special edition with our guests: Prithvi-Founder of Appiko Technologies, which works on wildlife conservation related technologies; and Murali-Founder of LionCircuits, which works in Electronics manufacturing space. The topic for today is Design for Manufacturing (DFM).
So Prithvi, Can you give us a quick overview of DFM?
Prithvi: So, DFM or Design for Manufacturing is the step that needs to be taken to optimize the design for manufacturing. Once you have a design that works as a prototype it does not necessarily mean that it will be easy to manufacture. There are many criteria that need to be considered for this; the two topmost are:
- Optimizing for cost
- Optimizing to reduce failures
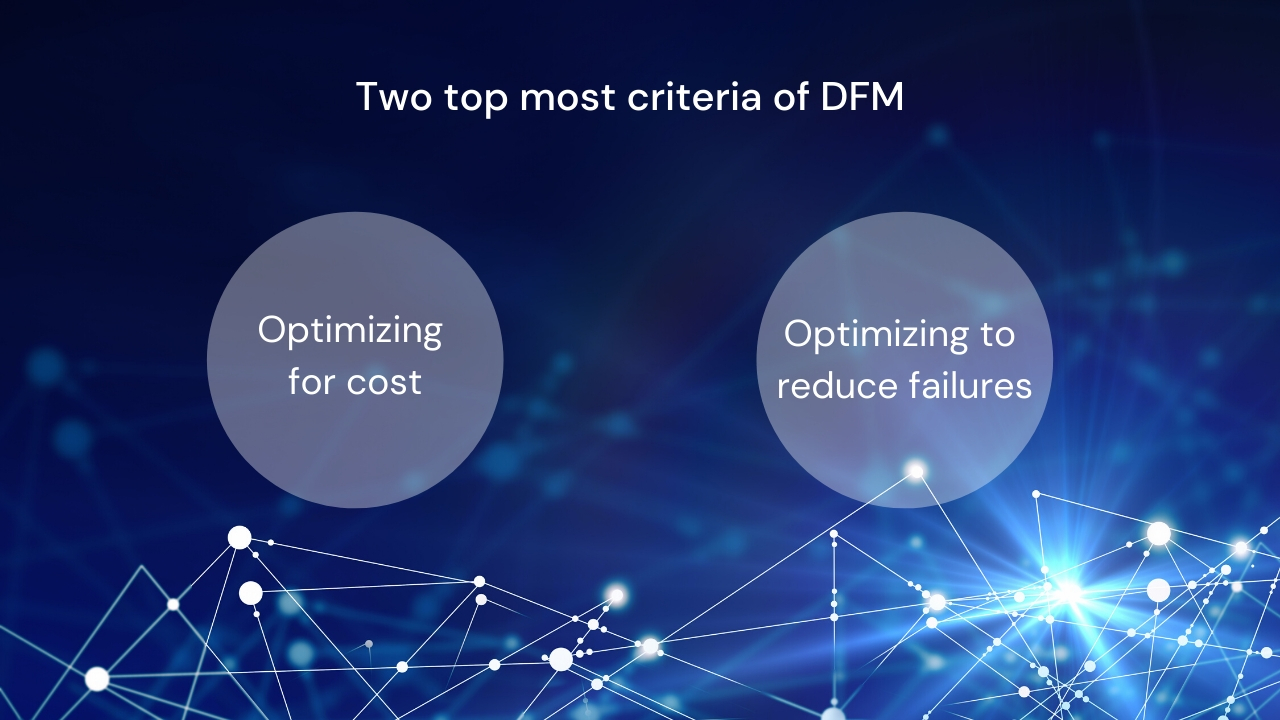
Anoop: Okay! So, from the optimizing cost perspective can you give us some examples?
Prithvi: Sure. For example, if you have a regulator and you are using a through-hole regulator for your prototype, it might be better to switch to an SMD regulator to reduce the cost in assembly for your product. Also, for example, if you have a filter that uses 150nf capacitor you might as well use the same capacitor in your decoupling capacitors. This way you are using the components and you can buy the same component in bulk to reduce the cost.
Anoop: So, essentially what you are saying is, I might have a design that is most optimal during a prototype but it might not be optimal from a cost perspective if we consider DFM.
Prithvi: Yes.
Anoop: Murali, we got to know about optimizing cost from a DFM perspective from Prithvi. Can you throw some light on predicting failures part of DFM?
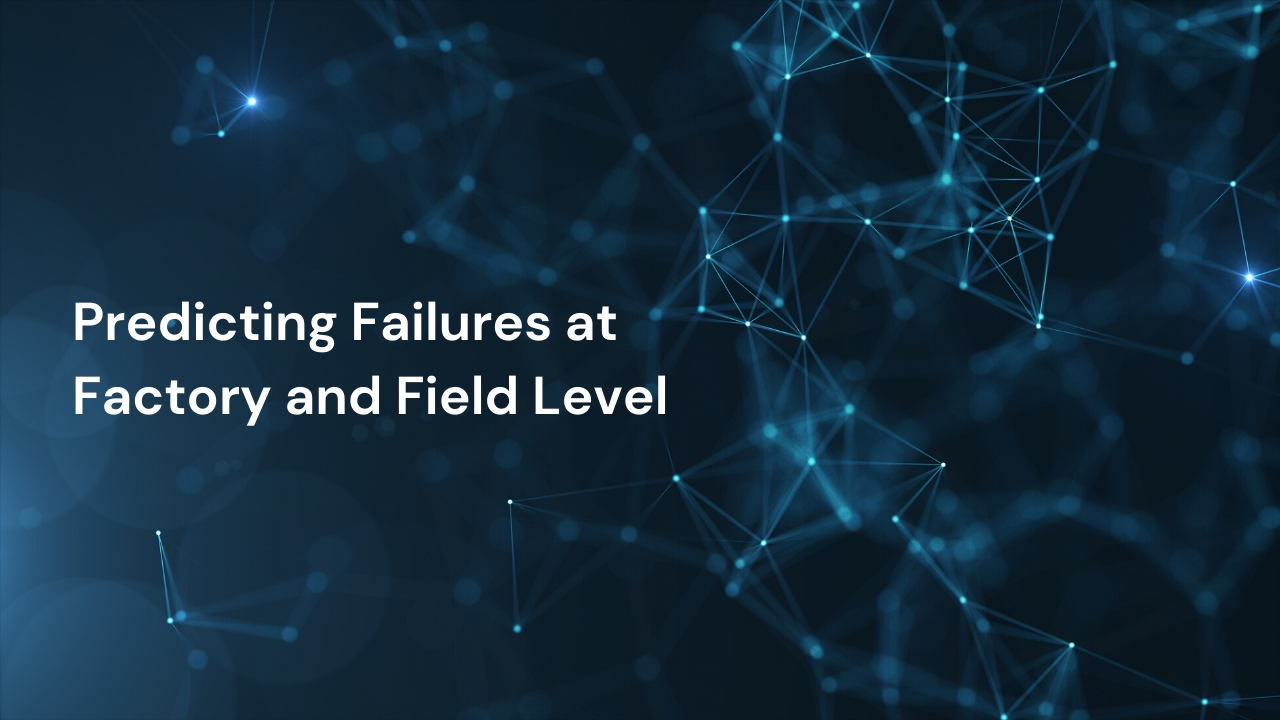
Murali: Sure. We can categorize predicting failures using DFM into two categories; one on the Factory Floor and the other one is on the Field. So there are certain things which we could predict in terms of Assembly failures or Fabrication failures, that we could take in design, it would be the Fab related DFM. The other is Field failures, such as, problems like vibration, or you know other failures that happen on the field.
Anoop: Okay! So, do you have any tools available which can help designers in analyzing or predicting some of these failures?
Murali: Yes. we at LionCircuits are working on two different tools:
For all the Fab related failures or Assembly related failures we have a tool called InstaDFM, which is an ML-driven algorithm runs on our cloud which improves with each and every design cycle that happens on our platform and with this we can predict failures that happen further down in the production cycle, way early in the process.
The second Tool is called ToolingAI. We use image processing based on the approach of AI algorithms that run on the cloud. With this, we can predict failures that are further down on the field by understanding the solderability (amount of solder on a board), and various other things like this are used to predict failures on the field.
Anoop: Interesting! Thanks for sharing light on predicting failures as a part of DFM, Murali.
So, Prithvi in DFM when do we start considering it as part of a product development process?
Prithvi: As the company grows I think it’s better to start inculcation DFM right in the prototype stage, as it becomes a company culture. Things that would help are having a known set of components and its footprints available as in the company repository and choosing the appropriate component right in the prototype stage so that it is also DFM friendly and also according to your specifications.
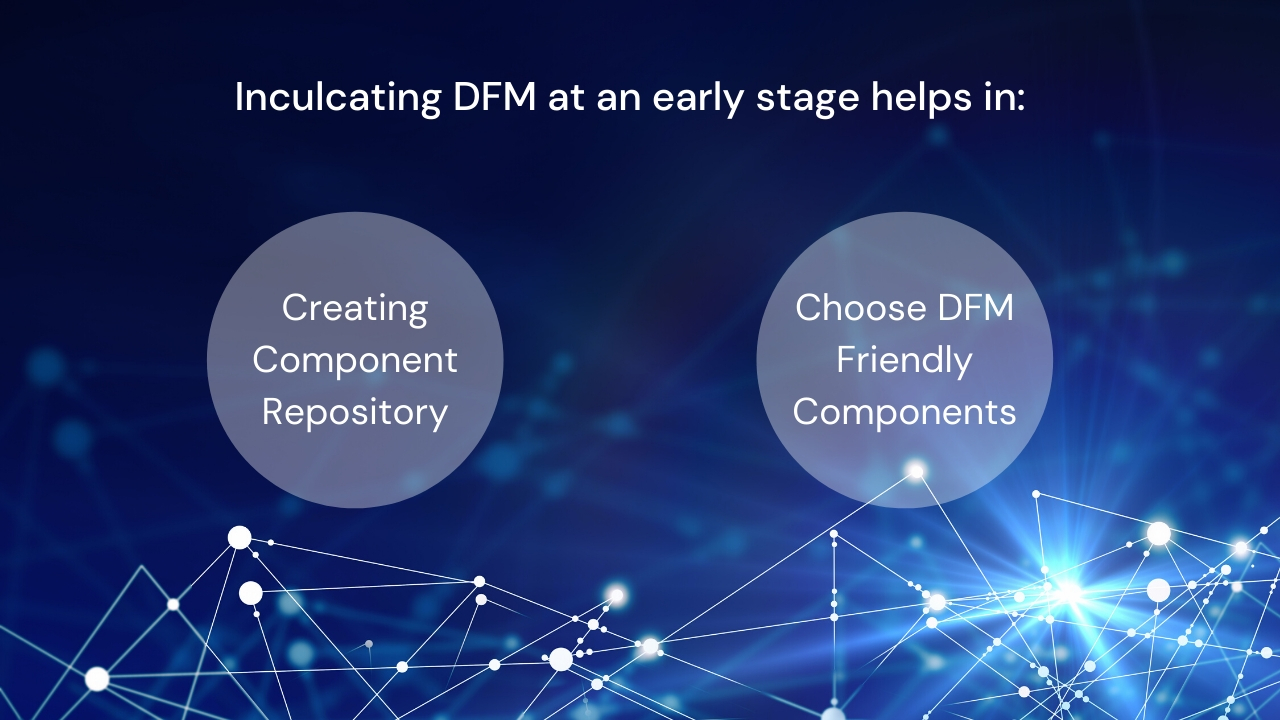
So, inculcating these at an early stage would help in the product development process.
Anoop: Great! So, folks, that was our enlightening session on DFM. Thankyou Murali and Prithvi.
